Understanding the Role of FR4 Material and Its Dielectric FR4 material is a crucial component in the world of electronics manufacturing, specifically for printed circuit boards (PCBs). Known for its excellent insulating properties and flame resistance, FR4 has become the industry standard for PCB substrates. This blog post delves into its technical aspects, advantages, and limitations, providing an in-depth understanding aligned with Google’s E.E.A.T principles.
What is FR4 Material?
FR4 is a grade designation for epoxy laminate sheets reinforced with woven fiberglass. The “FR” stands for “flame retardant,” and the “4” refers to the specific class of the material. It is composed of a woven glass-reinforced epoxy resin, creating a strong, lightweight, and highly durable material.
Key technical characteristics of FR4 include:
- High Dielectric Strength: Offers excellent electrical insulation.
- Moisture Resistance: Maintains integrity even in humid conditions.
- Thermal Stability: Withstands high temperatures without degrading.
- Mechanical Strength: Provides robust structural support for PCB components.
FR4 comes in various thicknesses and copper cladding options, making it versatile for single, double, and multi-layer PCBs.
Advantages of FR4 Material
- Cost-Effectiveness: Compared to other high-performance PCB materials, FR4 is relatively affordable, balancing performance and budget.
- Electrical Insulation: With high dielectric strength, FR4 prevents short circuits and enhances circuit reliability.
- Flame Resistance: Complies with UL94-V0 standards, meaning it self-extinguishes when a flame source is removed.
- Durability: The fiberglass reinforcement provides exceptional mechanical strength, crucial for handling complex PCB layouts.
- Ease of Manufacturing: FR4’s versatility simplifies the PCB fabrication process, allowing for rapid prototyping and mass production.
Limitations of FR4 Material
Despite its widespread use, FR4 does have its drawbacks:
- Thermal Limitations: FR4’s glass transition temperature (Tg) typically ranges from 130°C to 180°C. This makes it unsuitable for high-temperature applications like aerospace or automotive electronics.
- Signal Loss at High Frequencies: FR4 experiences dielectric loss, making it less effective for high-frequency circuits used in RF or microwave technologies.
- Moisture Absorption: While resistant to moisture, prolonged exposure can still slightly degrade its performance.
- Limited Heat Dissipation: FR4 doesn’t dissipate heat as efficiently as some advanced materials like ceramic or metal-core PCBs.
Applications of FR4 Material
FR4 is widely used across various industries, including:
- Consumer Electronics: Smartphones, laptops, and household appliances.
- Industrial Equipment: Control systems and machinery sensors.
- Automotive Electronics: Though limited to low-heat environments.
- Telecommunications: Low-frequency networking equipment.
Choosing the Right FR4 Grade for Your PCB
When selecting an FR4 material for your project, consider:
- Thickness: Ranges from 0.2mm to 3.2mm, depending on your PCB’s complexity.
- Copper Cladding: Options include 1oz to 3oz copper layers, affecting conductivity.
- Tg Rating: Ensure the glass transition temperature meets your thermal requirements.
Conclusion: Is FR4 the Right Choice for You?
By understanding both the strengths and limitations of FR4, you can make informed decisions tailored to your electronic design needs. Always consult with PCB fabricators and material experts to ensure you’re choosing the right substrate for optimal performance.
For more insights into PCB materials and design tips, stay tuned to our blog!
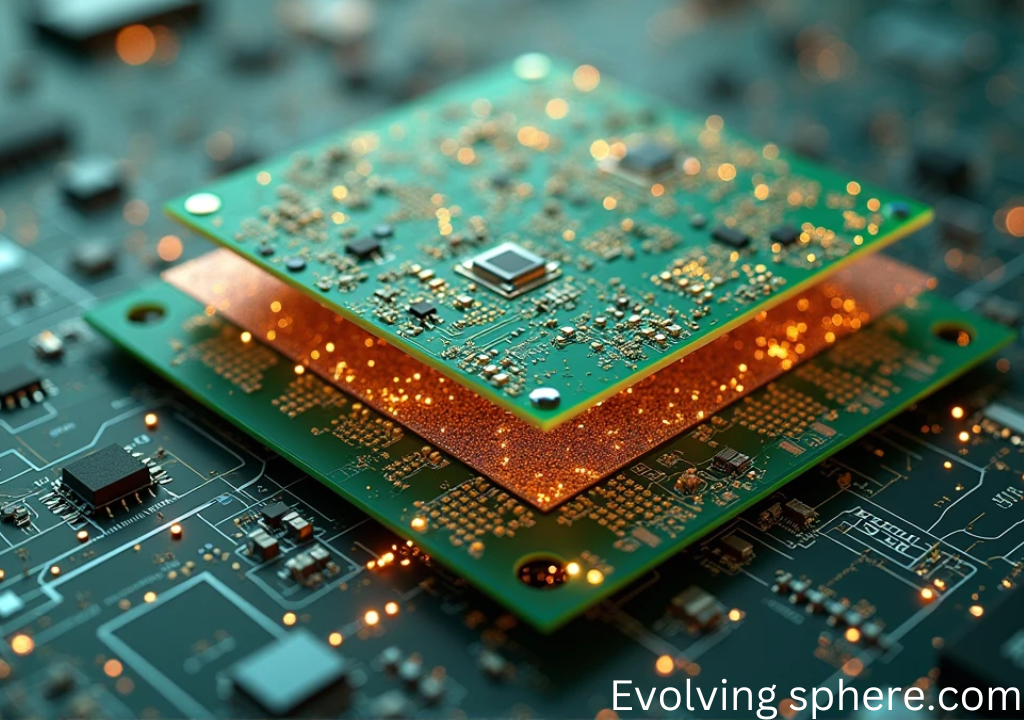
What is FR4 Material?
FR4, short for Flame Retardant 4, is a glass-reinforced epoxy laminate sheet used widely in the electronics industry. Known for its excellent strength-to-weight ratio, flame resistance, and electrical insulation properties, FR4 has become a go-to material for manufacturing printed circuit boards (PCBs).
Key Properties of FR4:
- High Dielectric Strength: FR4 offers strong electrical insulation, making it ideal for electronic components.
- Mechanical Durability: The material has high tensile strength, providing structural support for electronic circuits.
- Moisture Resistance: FR4 is highly resistant to water absorption, ensuring performance stability even in humid environments.
- Temperature Tolerance: It maintains integrity under high temperatures, crucial for electronic applications.
Common Uses of FR4:
- Printed Circuit Boards (PCBs): FR4 is the most common substrate in PCBs due to its electrical insulation and heat resistance.
Why Choose FR4?
FR4 strikes a balance between affordability, performance, and ease of manufacturing. Its flame-retardant properties and reliability under stress make it indispensable for modern electronic designs.
Whether you’re designing complex PCBs or need robust insulation material, FR4 offers a versatile and cost-effective solution.
FR4 Material: Frequently Asked Questions (FAQ)
Why is it called FR4?
The “FR” stands for “Flame Retardant,” and the “4” refers to the specific type of epoxy resin used. It meets the UL94V-0 standard for flame resistance, meaning it can self-extinguish once the flame source is removed.
What are the key properties of FR4?
- High dielectric strength (good electrical insulation)
- Thermal stability (resistant to heat and moisture)
- Mechanical strength (strong and durable)
- Lightweight
- Flame resistance
Is FR4 material waterproof?
While FR4 has low water absorption, it’s not entirely waterproof. However, its moisture resistance makes it reliable in most environments, unless prolonged exposure to water or extreme conditions occurs.
What temperatures can FR4 withstand?
FR4 typically withstands temperatures up to 130°C to 140°C (266°F to 284°F). For high-temperature variants, it can go beyond this range, but standard FR4 shouldn’t be used in extreme heat applications.
Is FR4 toxic?
In solid form, FR4 is safe and non-toxic. However, during manufacturing or cutting, dust particles can be hazardous if inhaled, so proper protective measures should be taken.
Can FR4 be machined or cut?
Yes! FR4 can be drilled, cut, and shaped, but it requires specialized tools due to its hardness and the presence of glass fibers. Always use proper dust extraction methods when working with it.
Is FR4 eco-friendly?
While FR4 offers durability, it’s not biodegradable. However, efforts are being made to develop more sustainable alternatives or recycling methods for electronic waste.
How does FR4 compare to other PCB materials?
FR4 is cost-effective, versatile, and reliable. Compared to high-frequency materials (like Rogers), it has lower thermal and electrical performance but is more affordable for general electronics.